
This approach is particularly of interest for the application of microfiltration and ultrafiltration in cases where dead-end operation is not possible due to the extent of membrane fouling. After the backwash, the flux is restored and normal filtration can continue. The wash water is collected as a waste fraction. After a certain time of regular operation, the effect of fouling becomes significant at this point, a backwash pump becomes active.
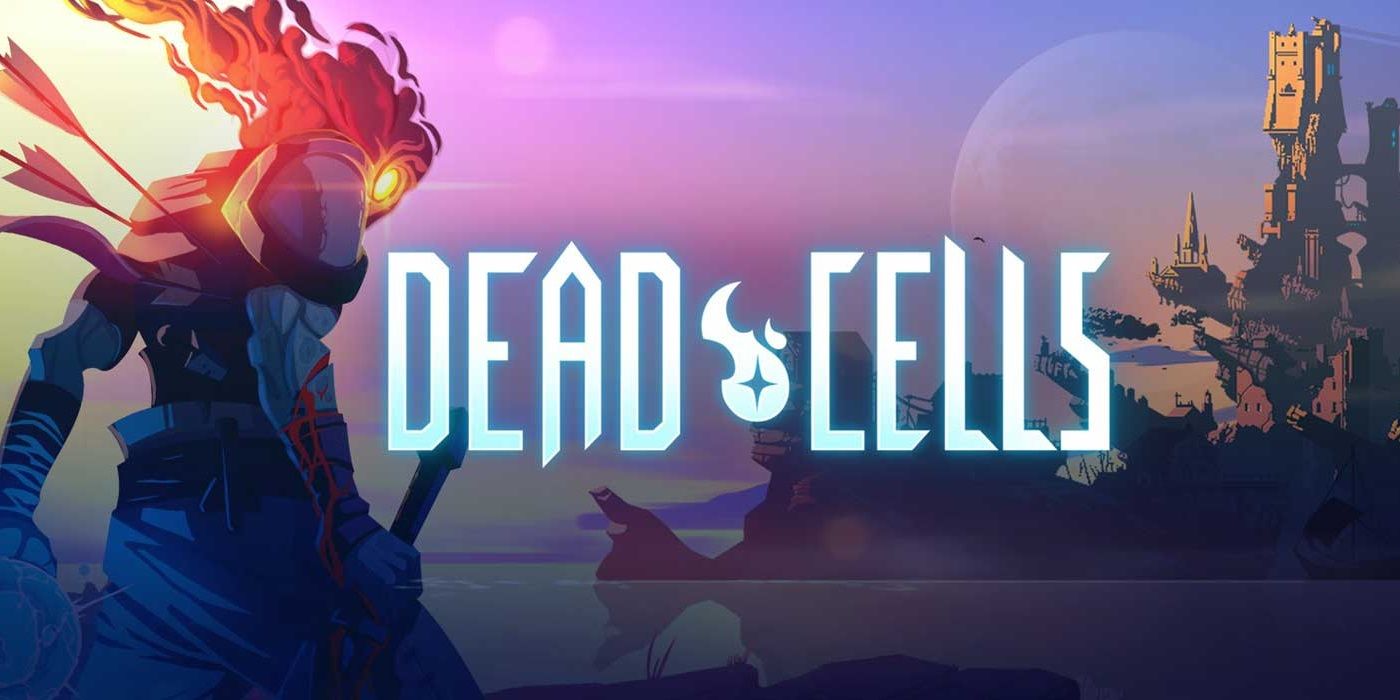
A semidead-end system relies on a periodical backwash, that is, a reversal of the flow direction so that permeate returns to the feed side through the membrane, thereby flushing away foulants that have accumulated in the pores of the membrane. This intends to combine the advantage of a dead-end system in obtaining a very high permeate yield, and the advantage of a cross-flow system in having a more efficient control of fouling. Conversely, ultrafiltration is typically applied in cross-flow mode, but may also be used in dead-end mode as a more economical method.Ī compromise between dead-end and cross-flow operation is a hybridization denoted as semidead-end operation. However, microfiltration may also be applied in cross-flow mode, for applications where the effect of fouling is too severe to apply dead-end filtration. Therefore this is the only filtration mode for reverse osmosis and nanofiltration.įor microfiltration the preferred operation mode is dead-end filtration, as it is the most economical strategy.

At the same time, effects of fouling and concentration polarization can be effectively kept under control in cross-flow filtration. Furthermore, the build-up of solute concentrations, salt concentrations in particular, would be too high for reverse osmosis when applied in dead-end mode this is also the case for nanofiltration.

The energy needed for circulating the feed relative to the energy needed for providing the transmembrane pressure is high for microfiltration for reverse osmosis, this is only a fraction of the required energy. Schematic representation of cross-flow filtration (A) for a flat sheet membrane and (B) for a tubular membrane. Among many types of housings available, the most common is the T-style, which is designed for installation into fixed piping systems, and is well suited for installation in filtration skids.įig. These cartridges come in standard lengths of 10, 20, 30, and 40 in., and are generally slightly less than 3 in. The filter housings typically used in manufacturing are designed to accept either single or multiple cartridges. Because the normal flow filters are usually available in finite size cartridges, the final sizing of a filtration step must account for the available cartridge configuration, including the filter housing aspect. Typically a safety factor of 1.5 is used, but larger safety factors can be applied if a more variable feed stream, such as harvested cell culture fluid, is used. With the minimum filtration area known, the final size of the filtration unit is determined by applying a safety factor to account for feed and membrane variability. Based on this assumption, a minimum filtration area necessary to accomplish a given filtration task within the time specified when operating at a given constant pressure can be calculated. Regardless of the method used to find out filter capacity, the scale-up is accomplished by assuming that between 50% and 80% of filter capacity ( V max) scales linearly with the filter area. Scalingup of a filter used in an application where the filtration is flux limited is fairly simple because of the assumption that filter performance scales linearly with filtration area is typically correct and the filter is sized based on the total volume to be processed and the processing time available for the filtration step (Eq. Typical experiments involve determination of flux, filter capacity, and step yield for a given feed stream. If heuristic information is not available, screening of different filters is the first step in designing a filtration step. Thus, should the filtration process be operated at constant pressure, the flow rate will need to be decreased to account for the increased fouling, and as such, flux will decrease as process time increases.ĭesign of a filtration step always starts with a decision over which type of membrane will be most effective for a given filtration task. Fouling increases pressure over the filter. Fouling will depend on solution composition, as well as on process conditions. Capacity, on the other hand, is related to the rate of fouling of the membrane. 32.2), depends on membrane permeability (a function of pore size distribution, porosity, and thickness), and on the solution properties (e.g., viscosity, density, and temperature). Eriksson, in Biopharmaceutical Processing, 2018 Normal Flow Filtrationĭead-end filtration applications can be divided into flux-limited and capacity-limited cases.
